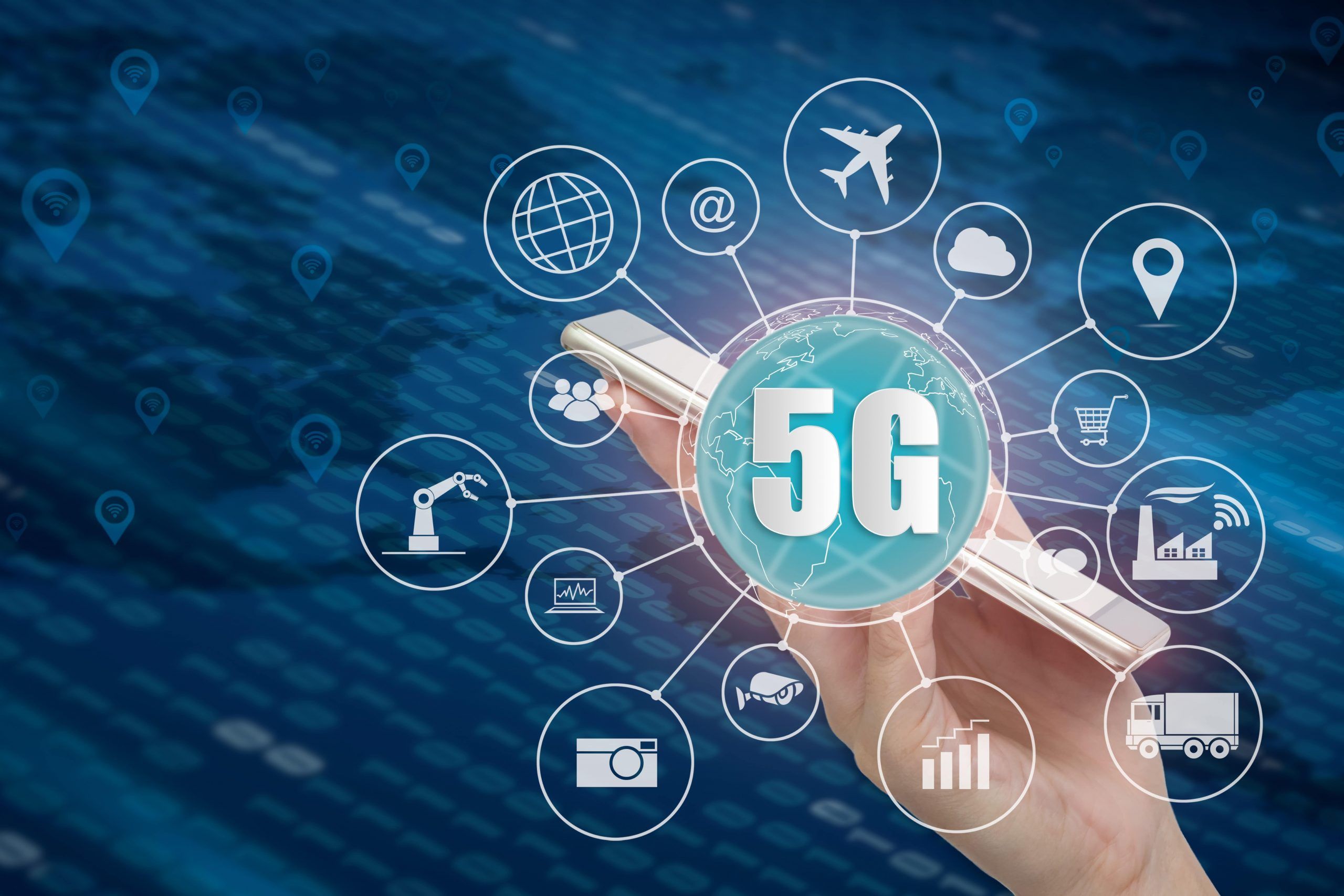
Digitalizzazione, produzione snella e 5G: come cambia la fabbrica di domani
Il mercato richiede tempi di risposta sempre più rapidi: monitoraggio e visualizzazione delle risorse di fabbrica possono incrementare efficienza e competitività e aiutano le imprese ad adeguarsi ai ritmi di un mondo dominato dal digitale. Ma un modello di fabbrica basato sull’analisi dei dati generati da tutta l’azienda non si improvvisa e richiede investimenti tecnologici e organizzativi.
Soprattutto l’evoluzione richiesta alle aziende manifatturiere impone che le produzioni diventino snelle (con la Lean production si riducono gli sprechi) e agili proprio grazie alla digitalizzazione. A supportare la trasformazione serve poi l’infrastruttura adeguata: il 5G, la quinta generazione di comunicazione mobile, è in grado di abilitare il cambiamento nella gestione dello scambio di dati e informazioni e da qui l’evoluzione dei processi, per esempio, di manutenzione, logistica, produzione…
Questi temi sono stati affrontati nel corso dell’evento dal titolo Produzione lean, digitalizzazione e 5G: accelerare la trasformazione digitale nella smart factory: si tratta del ciclo di incontri “5G Digitalization Roadshow”, promosso e organizzato dalla casa editrice ESTE (editore del nostro quotidiano): protagonista l’azienda veronese Exor International, che progetta e produce soluzioni di automazione industriale, ma che soprattutto è uno dei primi casi nazionali di sperimentazione 5G in ambiente produttivo. Dopo la tappa di Milano di fine ottobre, il 2 dicembre 2021 l’evento di sposta a Bologna.
CLICCA QUI PER INFORMAZIONI E PER ISCRIVERTI AL 5G DIGITALIZATION ROADSHOW
Proprio Exor International è un caso di grande interesse per le attività di digitalizzazione che sono state svolte all’interno dell’organizzazione: il 96% dei processi sono stati digitalizzati e l’obiettivo è di raggiungere la piena automazione, che si declina con la possibilità per i clienti di ordinare online i prodotti, di seguirne l’evoluzione e di riceverli nei tempi concordati. “Ogni passo che facciamo è indirizzato verso questa visione. Quindi, il primo è l’introduzione della Lean production, mentre poi serve concentrarsi sulla digitalizzazione e quindi sull’implementazione del 5G”, ha rivelato Mark Olding, Chief Commercial Officer di Exor International.
In realtà, come lo stesso manager ha spiegato, la riduzione degli sprechi in fabbrica è iniziata tempo fa; la pandemia ne ha ora accelerato l’adozione del modello, mettendo però in crisi quelle aziende che pur avendo introdotto le tecnologie più evolute non erano pronte per metterle realmente a valore in un momento complicato come quello dell’emergenza sanitaria. L’introduzione delle tecnologie, infatti, deve andare di pari passo con il cambiamento culturale dell’intera organizzazione: serve un cambio di mindset di tutti i lavoratori, dalla Direzione a chi è impegnato sulla linea di produzione.
Dare senso ai dati analizzandoli in modo diverso
Legata alla questione culturale c’è poi la valorizzazione dei dati, come ha chiarito Giuseppe Pace, CEO di Exor International: “La questione più importante è l’analisi del dato e la sua semplificazione per renderlo fruibile in Kpi”. E nel caso dell’azienda di Verona, Damiano Vendramini, Data Analyst Specialist, ha spiegato che è stata fatta una vera e propria raccolta dati centralizzata da utilizzare per la valutazione dei Kpi.
Ma questo non era ancora abbastanza, secondo lo specialista: i dati, in realtà, scattavano di fatto una fotografia del passato e non consentivano ancora di guardare al futuro. “Bisogna dare un senso al dato, fare in modo che sia un valore aggiunto perché un dato digitalizzato correttamente diventa un dato propositivo che stimola le persone”, è la tesi di Vendramini. Ecco allora che il cambio di mentalità resta il punto focale su cui concentrarsi: “Tutti sono chiamati a collaborare affinché l’azienda possa essere più efficiente, ma chiaramente non è semplice perché il cambiamento è sempre sconvolgente”.
Eppure è dai dati che prende il via la digitalizzazione, alla base dell’applicazione del modello di Industria 4.0. “Partendo dalla fabbrica, abbiamo riscontrato l’effettiva potenza del numero di dati che, una volta raccolti, possono essere analizzati e quindi funzionali per un miglioramento continuo”, ha continuato Pace. Il nuovo paradigma conduce anche alla creazione di nuovi modelli di business, in particolare su due fronti: la riduzione dei costi in fabbrica e il cambio di paradigma legato alle vendite.
Chi adotta nuove tecnologie e intraprende il percorso della trasformazione digitale deve mettere in conto di dover gestire alcuni aspetti da non sottovalutare; come ha spiegato il CEO di Exor International, per esempio, non bisogna temere di investire le risorse e di non ottenere poi i benefici sperati; e poi serve maturare la consapevolezza che non si può digitalizzare solo a livello tecnico. Ecco allora che la proposta è di porsi obiettivi ambiziosi, ma raggiungibili. “Serve applicare un approccio a piccoli passi, per costruire poco per volta la trasformazione, con la collaborazione di tutti”.
Garantire la connettività con il 5G
C’è infine – ma non è ultima in ordine di importanza – la questione della connettività: in questo caso è sempre più fondamentale la rete 5G (di cui abbiamo parlato nell’articolo La competitività passa dal 5G e durante il PdM Talk 5G: la tecnologia di nuova generazione che cambia le comunicazioni). “È un nuovo paradigma che consente di fruire contenuti in mobilità con una velocità 10 volte superiore al 4G”, ha affermato Alessandro Scatolini, Enterprise Marketing IoT e 5G di Tim. Inoltre il nuovo standard di comunicazione mobile abilita lo sviluppo di applicazioni verticali in settori chiave come Smart city, Industria, Automotive… “È una tecnologia che contribuisce alla digitalizzazione del Paese”.
Il 5G, infatti, permette di collegare tutto ad alta velocità e la rapidità abilita a nuovi business. Inoltre, le forti peculiarità della tecnologia di comunicazione supportano il tessuto industriale nello sviluppo di una connettività cui non si aveva mai avuto accesso prima. “Uno stabilimento dotato di rete 5G ha gli strumenti necessari per l’acquisizione dei dati sulla linea di produzione e l’implementazione dei modelli di business di Industria 4.0”, ha continuato Scatolini. Tradotto vuol dire che il 5G può penetrare negli oltre 150 distretti industriali del Paese e potenziare queste realtà che rappresentano circa un quarto del sistema produttivo del Paese. Inoltre la nuova tecnologia abilita un sistema aperto e una piattaforma che chiama la partecipazione di vari attori della filiera di produzione, generando quello che per il manager di Tim è un “grande vantaggio”.
Ma oltre alla capacità di banda, è necessario citare anche la sicurezza: il 5G è un protocollo sviluppato con i layer di sicurezza by design, e sulla base di logiche di network slice, reti che condividono la medesima infrastruttura fisica di accesso e trasporto, per supportare diversi casi applicativi con caratteristiche e requisiti particolari. Questa infrastruttura garantisce una maggiore flessibilità, un uso efficiente delle risorse e maggiori opportunità di business.
Nell’era tecnologica è necessario dunque intraprendere un percorso di digitalizzazione che contempli l’implementazione delle nuove tecnologie, ma anche un cambio culturale all’interno dei processi organizzativi.
Laureata magistrale in Comunicazione, Informazione, editoria, classe di laurea in Informazione e sistemi editoriali, Federica Biffi ha seguito corsi di storytelling, scrittura, narrazione. È appassionata di cinema e si interessa a tematiche riguardanti la sostenibilità, l’uguaglianza, l’inclusion e la diversity, anche in ambito digital e social, contribuendo a contenuti in siti web.
Ha lavorato nell’ambito della comunicazione e collabora con la casa editrice ESTE come editor e redattrice.
industria 4.0, tecnologia, 5G, este, Exor International
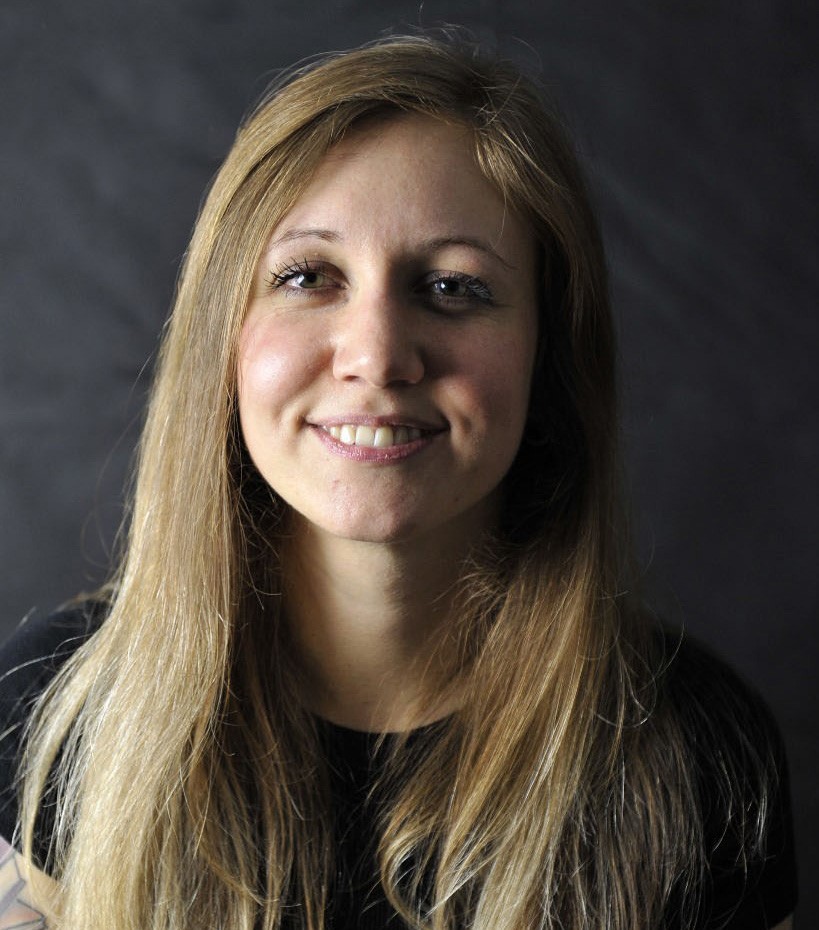