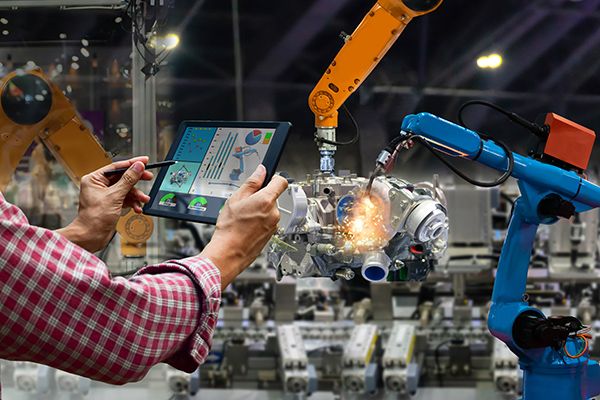
Chi dice che non si può fare Smart working in fabbrica?
Grazie al digital twin anche la produzione si aggiorna. Ma servono le competenze.
Di tecnologie digitali in fabbrica se ne parlava ben prima della pandemia da Covid-19; l’emergenza sanitaria, si sa, ha accelerato in modo netto l’interesse per questi strumenti: se fino a ieri abbiamo assistito a una lenta adozione delle tecnologie digitali, proprio perché ne stiamo toccando con mano il potenziale, oggi si è diffusa la certezza di non poterne più fare a meno.
Durante la tappa di Bologna di FabbricaFuturo, il progetto multicanale della casa editrice ESTE, promosso dalla rivista Sistemi&Impresa e di cui Parole di Management è Media Partner, Marco Taisch, Professor of Operations Management and Advanced & Sustainable Manufacturing System al Politecnico di Milano e membro del Comitato Scientifico della rivista della casa editrice ESTE Sistemi&Impresa, ha fatto notare che la lenta adozione delle tecnologie in fabbrica ha fatto perdere competitività a tante aziende. Ora, tuttavia, lo scenario è profondamente mutato e nella pandemia lo stress test relativo allo Smart working – o meglio Remote working, perché è stato ben lontano dalla leva organizzativa alla base del lavoro agile – ha dimostrato come proprio le tecnologie consentono di ottenere maggiore efficienza.
Secondo Taisch, che, tra le varie cariche, è anche Presidente del Competence Center Made, quella che stiamo vivendo è una grande opportunità; addirittura la definisce come una “disruption storica”, paragonabile a quelle del passato, come il cambiamento delle procedure di sicurezza del trasporto a seguito dell’attacco alle Torri Gemelle oppure il boom dell’ecommerce dopo l’esplosione della Sars nel 2003. Per l’esperto, l’attuale situazione impatta su quattro aree: l’estensione dello Smart working in fabbrica; l’allineamento delle competenze 4.0; i nuovi modelli di business; il ridisegno delle Operations, dei layout di fabbrica e della Supply chain.
Digital twin e competenze come fattori abilitanti
Di Smart working se n’è parlato ampiamente in questo periodo. Prima del Coronavirus, il lavoro agile interessava il 2,2% dei lavoratori, contro circa il 25% di marzo 2020, equamente divisi tra dipendenti pubblici e privati; a oggi gli ultimi dati indicano che svolgono Smart working circa 8 milioni di persone, pari al 44% della forza lavoro. Parlare di Smart working in fabbrica può sembra un controsenso, ma così non è se si pensa che a fronte di ruoli che impongono la presenza fisica negli impianti produttivi, ne esistono altri che possono essere svolti da remoto. È il caso, ricorda Taisch, della manutenzione, ma pure della Qualità.
Ad abilitare la nuova forma di lavoro è il digital twin, il gemello digitali di prodotti e processi che permette di gestire le informazioni anche lontano dalla fabbrica. Seguendo il ragionamento, dunque, è ipotizzabile che i layout degli spazi di produzione siano destinati a cambiare e non per forza perché la componente umana è prossima a farsi sostituire dai robot: già oggi le fabbriche devono assicurare il distanziamento sociale e l’applicazione del lavoro da remoto può agevolare anche il rispetto delle nuove norme.
Cambiare il modello di lavoro, però, impone l’aggiornamento delle competenze, che restano al centro dell’attenzione. Se i dati abilitano nuovi modi di lavorare anche in fabbrica, è necessario che tutte le figure professionali coinvolte nei processi siano adeguatamente formate per espletare la propria innovativa mansione. Questo implica, inoltre, che siano assunte decisioni anche ai livelli più operativi e non per forza strategici: significa introdurre logiche lean in fabbrica, con la trasformazione dei blue collar in personale qualificato per gestire i dati.
Collaudo a distanza e Supply chain più resilienti
Sul fronte dei modelli di business, Taisch non ne vede di nuovi all’orizzonte. Piuttosto, ragiona, è il momento per concretizzare quelli già noti e che da tempo avevano individuato nella remotizzazione dei potenziali di sviluppo. È il caso del collaudo di macchinari a distanza: il docente del Politecnico ricorda che proprio durante il lockdown ci sono stati casi di gestione da remoto degli impianti e ora che stiamo andando verso una ‘nuova normalità’, chi ha sperimentato l’innovazione difficilmente tornerà indietro, perché è stato dimostrato che c’è una valida alternativa al modello tradizionale di lavoro (inoltre i costi sono nettamente inferiori).
Lo stesso Presidente del Made prova a suggerire altri trend che, a suo giudizio, potrebbero presto imporsi. Per esempio, il ‘noleggio’ degli impianti produttivi, che consente di esternalizzare la produzione e di modularla rispetto alle necessità, pagando l’uso dei macchinari: è noto il caso dei motori Rolls Royce per gli aerei, che sono ‘noleggiati’ dalle compagnie e pagati a ore di utilizzo con il modello pay per use.
Infine c’è il capitolo che riguarda il ridisegno delle Operations e delle catene di fornitura. Come spiega Taisch, ormai le Supply chain sono disegnate a livello mondiale – una scelta imposta nel passato per la riduzione dei costi – ma la pandemia ne ha svelato i limiti: le catene di fornitura sono, infatti, andate in sofferenza a seguito delle chiusure imposte dall’emergenza sanitaria e la riapertura ‘sfalsata’ di regioni e Paesi diversi ne conferma le difficoltà. Ecco perché il docente invita a disegnare Supply chain più resilienti: tra le direzioni proposte, di certo c’è quella di renderle più corte e più locali.
competenze, Smart working, Supply chain, fabbrica, digital twin
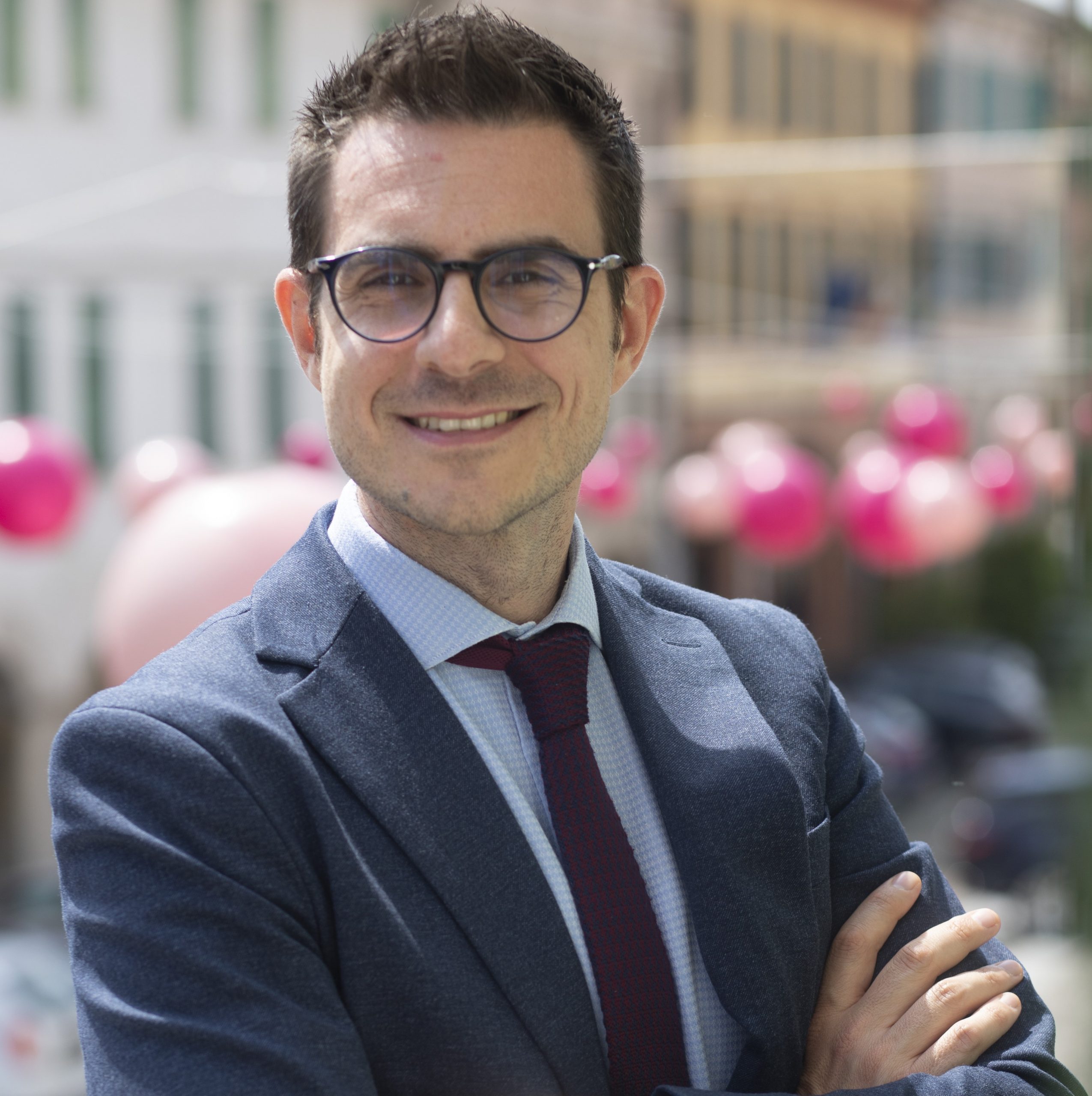