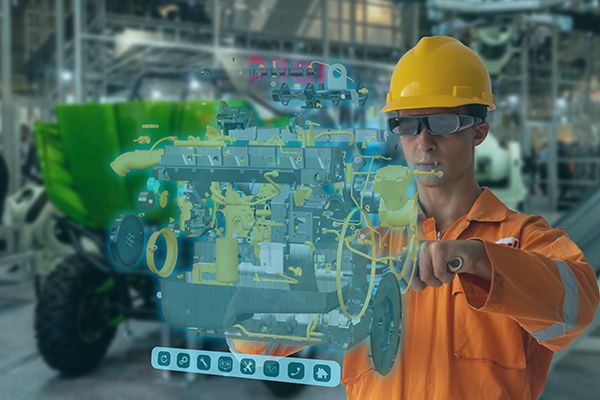
Il digital twin trasforma il Manifatturiero 4.0
Dopo l’iniziale timore nei confronti di una pandemia che avrebbe potuto mettere in ginocchio il settore manifatturiero, l’Italia sta assistendo a un momento di inattesa crescita. A dirlo è il Purchasing Managers Index (PMI), indicatore economico che attraverso rapporti e sondaggi mensili in seno alle aziende private del Manufacturing mostra lo stato di salute dell’economia del Paese: a maggio 2021 si è saliti sopra quota 53 (sotto la soglia pari a 50 si parla di recessione), con l’Italia che si sta dimostrando più effervescente e reattiva di quanto previsto. Complice della crescita, forse, anche la digitalizzazione.
Secondo Giuliano Busetto, Head of Digital Industries di Siemens Italia (che ha presentato in una recente conferenza stampa l’impegno dell’azienda nel supporto delle aziende manifatturiere verso la Digital Transformation), anche se siamo indietro rispetto agli altri Paesi, sia sull’integrazione delle tecnologie digitali sia sull’utilizzo di Internet, abbiamo un solido piano di Transizione 4.0. “Nei prossimi anni il mercato, pur fronteggiando sfide difficili, si saprà di certo adattare alla flessibilità, all’alta qualità e all’efficienza richieste, con un occhio su ambiente e sicurezza”.
La digitalizzazione, quindi, diviene strumento prezioso per aumentare produttività, flessibilità, efficienza del time to market (dimezzando i tempi di sviluppo dei prodotti) e sostenibilità ambientale, rendendo le imprese manifatturiere al passo con i tempi. Il modo migliore per farlo? Per Busetto è collegare le linee produttive fisiche (sempre più automatizzate) a quelle virtuali, creando per ogni processo produttivo fisico un gemello digitale (digital twin). “Ogni componente di processo può avere la sua rappresentazione virtuale, dal pezzo unico di una bottiglietta fino alle decine di migliaia di quelli che formano un’automobile, con la possibilità di lavorare su ogni singola parte da più postazioni distanti nell’azienda e nel mondo e realizzando l’oggetto nella sua interezza”. Inoltre il digital twin permette di valutare in anticipo fattibilità, rischi e risultati finali, prevedendo gli errori e organizzando preventivamente anche l’interazione uomo-macchina.
Nel futuro AI, Edge computing e… giovani menti
Pensare che il Manifatturiero sia solo fisico e analogico, quindi, è sbagliato. Le tecnologie digitali applicate al settore continuano a svilupparsi e implementarsi: l’Intelligenza Artificiale (AI), ma anche l’Additive manufacturing, il Cognitive engineering, l’Internet of Things, la tecnologia Blockchain, il 5G industriale… Il futuro più prossimo è già segnato e le industrie manifatturiere possono dunque pensare a investimenti mirati per rendere più efficienti, efficaci e sicuri tutti i processi interni. Le tecnologie su cui puntare oggi? Per Busetto sono la realtà aumentata, l’AI e l’Edge computing, ovvero l’intelligenza locale con un modello di calcolo distribuito per elaborare i dati il più vicino possibile a dove questi dati vengono richiesti.
A sostenere le imprese in questo investimento ci penserà, tra gli altri, il Recovery Fund. “Con la legge di Bilancio 2021 potremo avere una grande spinta verso la digitalizzazione, rendendo interessanti e affidabili le aziende italiane e quindi l’Italia stessa”, spiega Busetto. “Importante, però, è investire non solo nelle tecnologie, ma anche nei giovani ingegneri, che, aggiornati, renderanno competitive le imprese in cui lavoreranno”.
Accanto a questi, il settore industriale deve tuttavia puntare sul cambio di mentalità generale. “L’interesse del settore industriale verso la digitalizzazione esiste. La parte più difficile non è tuttavia il punto di vista tecnico, ma il cambio di mentalità a tutti i livelli di un’organizzazione, prendendo tempo per spiegare i motivi del cambiamento e coinvolgendo i collaboratori. Il successo dipende infatti da quanto le persone condividono il progetto”, ha fatto notare Andrés Cartagena Ruiz, Head of MFL X di Mario Frigerio Group, intervenuto nella conferenza stampa promossa da Siemens. A suo giudizio questo compito non deve essere affidato ai dipartimenti esistenti, già impegnati nei loro progetti e nei loro compiti, ma ad un team dedicato che si concentri su questa trasformazione interna. “E, infine, bisogna saper scegliere partner (fornitori, ma anche investitori, soci e clienti pilota) che credano nel progetto e abbiano lo stesso scopo”.
Dello stesso avviso è Max Panaro, ICT & System Quality VP per il Gruppo Maire Tecnimont – anche lui accanto a Busetto nella conferenza stampa di Siemens – secondo il quale il successo della trasformazione 4.0 delle aziende manifatturiere italiane dipende anche dall’allineamento di tre prospettive. Innanzitutto, gli operatori sul campo devono aumentare la produttività abbracciando la trasformazione; i collaboratori devono poi avere a disposizione degli strumenti avanzati e artificialmente intelligenti fatti apposta per l’ambito industriale (e non tecnologie esistenti pensate per altri settori); e infine prevedere, all’interno del sistema, un’integrazione reale, con un team specializzato che conosca tanto il funzionamento dell’impianto quanto le licenze e le implicazioni digitali.
Sara Polotti è giornalista pubblicista dal 2016, ma scrive dal 2010, quando durante gli anni dell’Università Cattolica del Sacro Cuore (facoltà di Lettere e Filosofia) recensiva mostre ed eventi artistici per piccole testate online. Negli anni si è dedicata alla critica teatrale e fotografica, arrivando poi a occuparsi di contenuti differenti per riviste online e cartacee. Legge moltissimo, ama le serie tivù ed è fervente sostenitrice dei diritti civili, dell’uguaglianza e della rappresentazione inclusiva, oltre che dell’ecosostenibilità.
digitalizzazione, Siemens, digital twin, tecnologie digitali
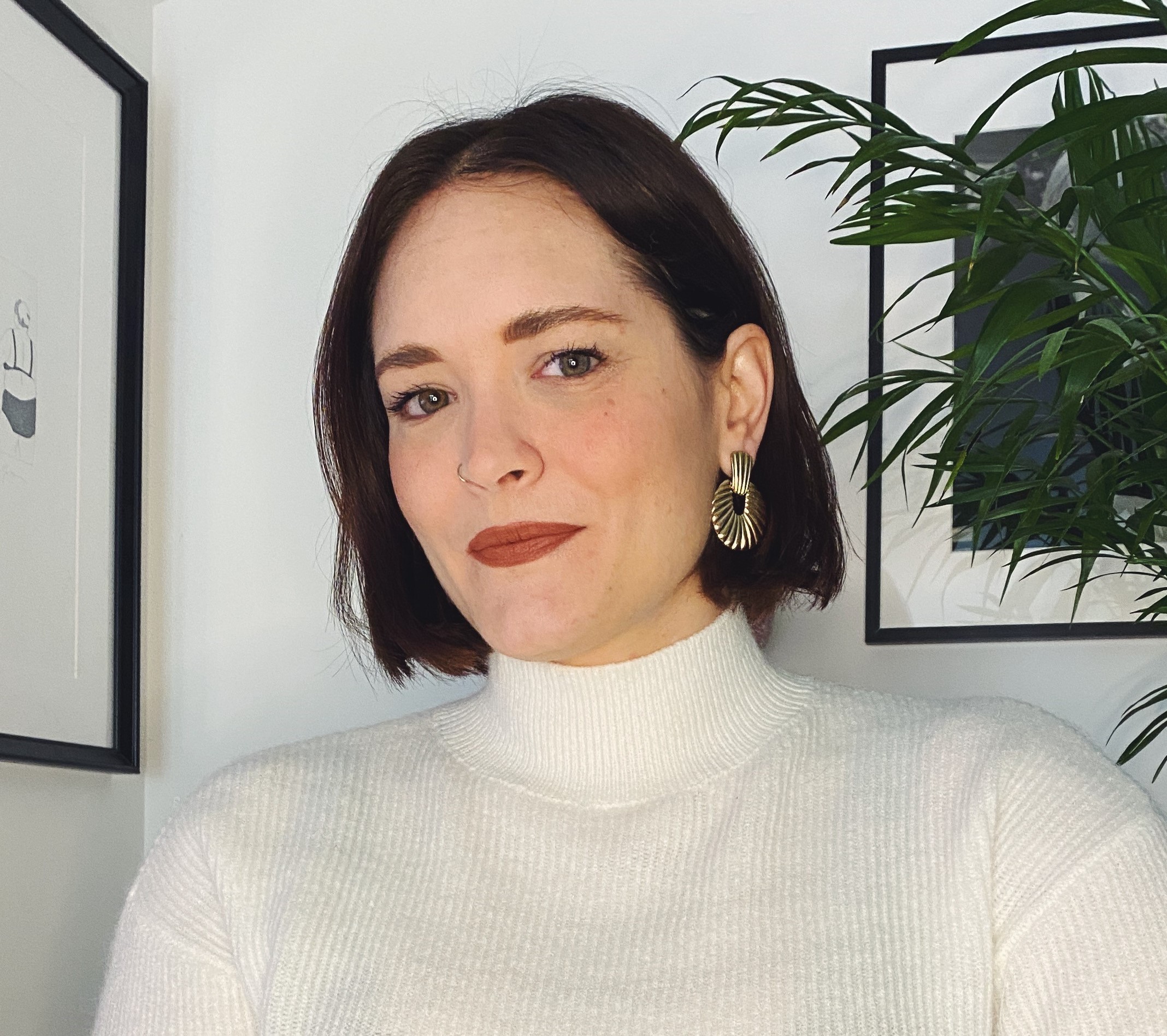