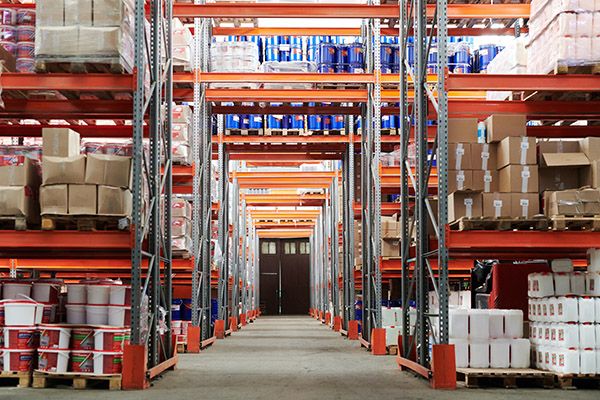
Prevedere e pianificare per governare il futuro della fabbrica
Le aziende che hanno usato i dati hanno saputo ridisegnare le catene di fornitura e incrementare i processi.
L’emergenza sanitaria ha messo sotto stress le aziende. Alcune, però, si sono dimostrate in grado di reagire alla situazione meglio di altre. Si tratta di quelle organizzazioni che avevano già sviluppato un progetto di interconnessione tra le fasi del processo di produzione ben prima dell’avvento del Covid e che hanno saputo mettere al centro i dati. Hanno usato, cioè, le informazioni per gestire l’attualità e immaginare nuovi scenari.
“Alcune imprese in effetti sono riuscite a fronteggiare abbastanza agevolmente la situazione perché avevano già adottato gli strumenti che hanno poi permesso di garantire flessibilità durante le operazioni e soprattutto la capacità non solo di saper operare, ma anche di programmare le attività”, ha detto Simone Marchetti, Digital Supply Chain e Sales Development Manager Italy di Oracle, intervenendo alla tavola rotonda promossa dalla casa editrice ESTE (editore di Parole di Management) Le chiavi per governare il futuro della fabbrica: innovazione tecnologica e un nuovo sguardo al business.
Con una diffusione rapida e geograficamente complessa della pandemia, i modelli si sono riconfigurati in fretta. Le aziende hanno ridisegnato le proprie catene di fornitura e hanno lavorato per incrementare i processi in vista di un modo nuovo di operare e produrre. La Logistica è diventata un differenziale di competitività: chi è riuscito a garantirne l’efficienza ha potuto mantenere o migliorare la sua posizione sul mercato. “All’inizio del 2020 abbiamo parlato di come ottenere resilienza all’interno delle organizzazioni, oggi si tratta di andare oltre questo concetto e usare le Operation come strumento di crescita e competitività”, ha continuato Marchetti.
Pianificazione integrata per rispondere a bisogni nuovi
La chiave del successo, soprattutto nei momenti di difficoltà, è la capacità di assecondare il passo del cambiamento. “Occorre essere veloci e prendere decisioni allineate con le aspettative che i mercati e le normative impongono. Per questo in Oracle lavoriamo molto con la comunità di aziende clienti, che partecipano attivamente alla fase di sviluppo delle nuove funzionalità e ci indicano la direzione che vogliono prendere”.
La maggiore difficoltà che le imprese italiane stanno fronteggiando è forse rappresentata proprio dalla grande incertezza che si riflette sull’organizzazione aziendale. Il Manufacturing ha la necessità di prevedere e pianificare, soprattutto in ambito produttivo. “Da anni si stanno digitalizzando i processi, ma manca spesso la parte di pianificazione, che non può più essere a compartimenti stagni, ma dev’essere integrata tra le diverse aree aziendali”, ha spiegato Stefano Betti, Application Sales Representative di Oracle.
Pianificare l’uscita delle merci coordinata con il forecasting delle vendite, ridurre al minimo la differenza tra produzione e vendita, eliminare lo scarto tra pianificazione della produzione e previsione della domanda. Le esigenze delle aziende oggi passano tutte per l’analisi di diversi scenari e chiamano in campo le potenzialità di Machine learning e Intelligenza Artificiale per capire come questi muteranno al cambiare di determinate variabili. Una necessità nuova, nata in epoca Covid, si colloca a metà strada tra il planning e il Risk management: è l’esigenza di prevedere l’impatto di una calamità sul singolo plant o sulla singola region dell’impresa per decidere come intervenire.
Una contaminazione positiva tra progettazione e manutenzione
Le organizzazioni, insomma, stanno iniziando a fare i conti con l’imprevedibilità. “Abbiamo imparato negli anni a essere molto flessibili”, ha raccontato Valentina Colaiacolo, General Manager Manufacturing Excellence di Wartsila, azienda finlandese specializzata nella fabbricazione di sistemi di propulsione e generazione d’energia per uso marino e centrali elettriche. “A marzo 2020 abbiamo dovuto tirare il freno a mano, ripianificare la produzione e cancellare ordini. È stata dura, ma eravamo già abituati a tempi order to delivery sempre più sfidanti e a target sempre più ridotti. Abbiamo puntato ancora di più sulla digitalizzazione in tanti settori, dagli audit all’acceptance test dei motori”.
La sede triestina di Wartsila ha lavorato a lungo sull’ottimizzazione dei processi con un approccio basato sull’operational excellence, prima di introdurre le prime tecnologie 4.0 tre anni fa. Tutto sviluppato internamente: dal Dot Connector, una sorta di Mes connesso alle macchine, ad applicazioni web e sistemi di gestione dati. “Piccole innovazioni create direttamente sul campo e sviluppate in casa”, ha puntualizzato Colaiacolo.
Secondo la manager, il merito è anche della strategia di coinvolgere persone esterne all’ufficio Innovazione: operai, dipendenti e manager di ogni funzione sono chiamati a collaborare, per creare una contaminazione positiva tra tecnologie standard e campi attenti alla qualità. In Wartsila esiste un X Team dedicato all’innovazione, un gruppo “un po’ carbonaro”, secondo la definizione della manager, che unisce ingegneria di produzione e manutenzione per ridurre il gap culturale tra le diverse posizioni.
Curare la gestione del dato su produzione e vendite
Anche chi ha attraversato la prima ondata pandemica senza stop di produzione ha dovuto fare i conti con una situazione nuova. E con la pressione di chi sa di non potersi fermare. È stato così per Mutti, storica azienda di conserve di pomodoro, che ha visto aumentare i volumi delle vendite e ha dovuto rivedere la pianificazione della produzione. “Durante il primo lockdown la nostra preoccupazione era rivolta all’estate: siamo un’azienda a forte carattere stagionale, perché la trasformazione della materia prima è concentrata nel periodo estivo”, ha spiegato Giorgio Lecchi, Industrial Director di Mutti.
Proprio perché in soli 70 giorni si decide un anno di lavoro, va evitato qualsiasi ritardo o intoppo del processo. Da quando l’azienda ha cominciato a crescere una decina anni fa, Mutti ha iniziato a curare la gestione del dato, sia a consuntivo sia in tempo reale. Oggi lavora per farlo anche verso l’esterno, lato domanda e lato fornitori. “È sempre più importante integrarsi perché i tempi tenderanno a comprimersi”.
Durante l’emergenza, la pianificazione delle produzioni si è scontrata con la necessità delle vendite. Entrambi i livelli di pianificazione sono stati rivisti: quello della campagna di trasformazione, articolato su due anni, e quello delle vendite, che segue una programmazione annuale e mensile. Due piani diversi, ma legati tra loro, perché se non si trasforma il pomodoro durante l’estate non si può vendere in inverno. “La Pianificazione, insieme con la Logistica, è l’area che ha dovuto sopperire ai volumi in forte aumento. Avere una logistica tutta interna, con un controllo diretto delle operazioni, ci ha avvantaggiato: con una disponibilità della materia prima a 100 chilometri dallo stabilimento, non abbiamo avvertito il problema dell’approvvigionamento”, ha ricordato Lecchi. Mutti punta oggi ad avere maggiore visibilità sui volumi dei raccolti e sulla tracciabilità del prodotto, anche grazie alle prime sperimentazioni di realtà aumentata. L’obiettivo è il forecasting della materia prima più che delle vendite.
Governare i diversi plant grazie all’integrazione
La gestione della domanda è stata estremamente critica e nervosa, perché soggetta a cambiamenti nel breve termine, anche per Sews Cabind, azienda specializzata nello sviluppo e nella produzione di cablaggi per veicoli industriali. Con 25 fornitori diretti che consegnano su sette plant produttivi, le difficoltà produttive e logistiche a monte hanno richiesto di poter integrare la previsione della domanda con quelle a breve termine della fornitura.
“A ciò si aggiunga il fatto che, essendo un’azienda che non produce in Italia, ma in Messico, Albania, Marocco, resta fondamentale governare le diverse fabbriche. L’integrazione era già parte del processo”, ha detto Antonio Nicola, Corporate Production Planning & Logistic Director di Sews Cabind. “È stato un periodo estremamente critico per la fornitura, la variabilità dei plant, i picchi di assenteismo e la difficoltà gestionale di dover organizzare turni di produzione e poterli controllare in real time”.
Sul fronte delle previsioni, ci si scontra anche con la variabilità delle richieste dei clienti: le esigenze sono sempre di più, in tempi sempre più stretti. Al di là della possibilità di intercettare i cambiamenti con algoritmi ogni giorno più precisi, occorre anche dotarsi di strumenti interni che rendano l’organizzazione più robusta e accettare la variabilità della domanda. “La vicinanza al dato e all’informazione è l’unica cosa che può fare la differenza. Oggi c’è il rischio di perdere la vicinanza al processo produttivo, invece è lì che bisogna cercare di lavorare di più”.
Articolo a cura di
Giornalista professionista dal 2018, da 10 anni collabora con testate locali e nazionali, tra carta stampata, online e tivù. Ha scritto per il Giornale di Sicilia e la tivù locale Tgs, per Mediaset, CorCom – Corriere delle Comunicazioni e La Repubblica. Da marzo 2019 collabora con la casa editrice ESTE.
Negli anni si è occupata di cronaca, cultura, economia, digitale e innovazione. Nata a Palermo, è laureata in Giurisprudenza. Ha frequentato il Master in Giornalismo politico-economico e informazione multimediale alla Business School de Il Sole 24 Ore e la Scuola superiore di Giornalismo “Massimo Baldini” all’Università Luiss Guido Carli.
oracle, pianificazione, Mutti, dato, produzione, Wartsila, Sews Cabind
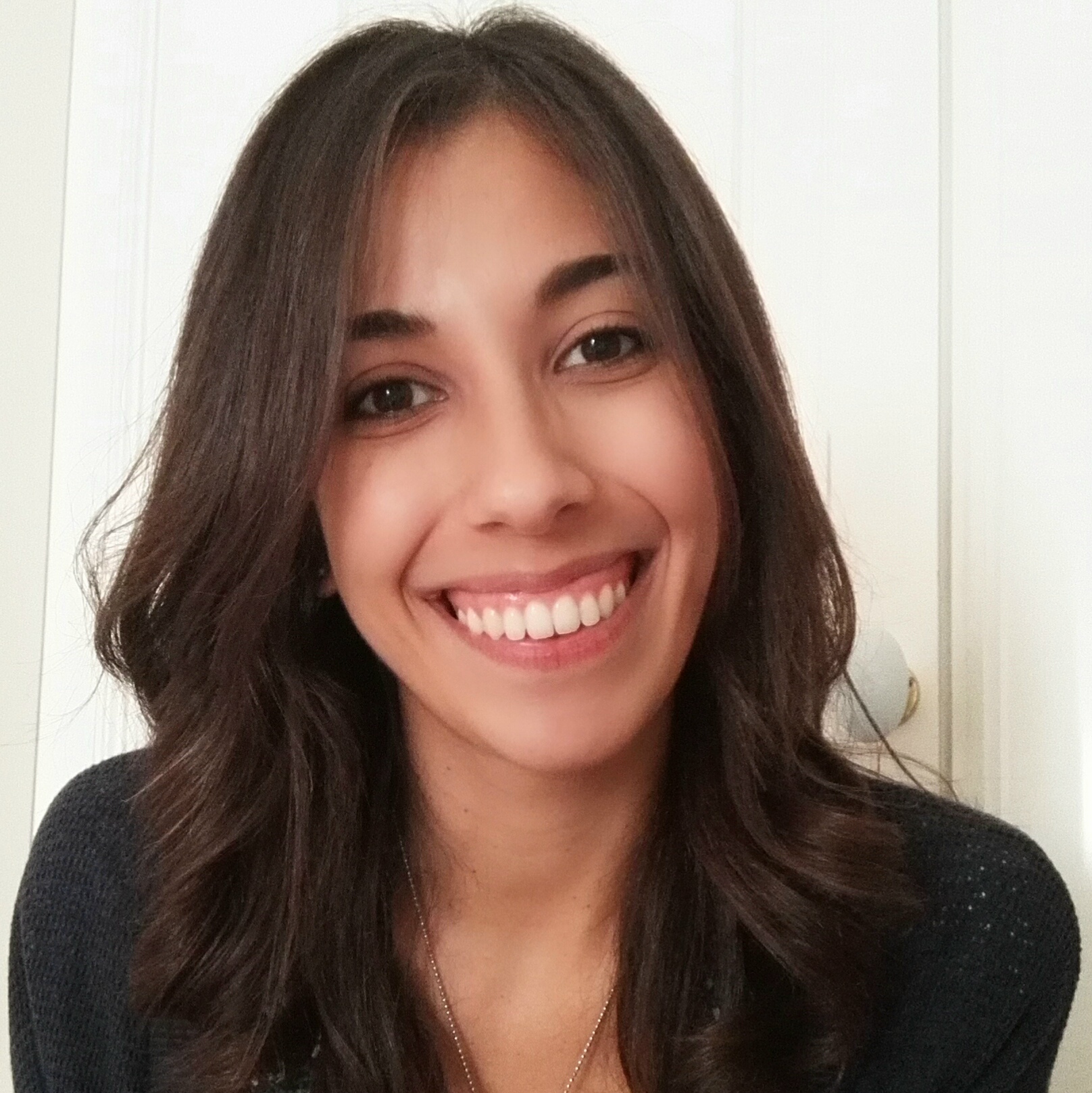